Evaluating the performance and reliability of an item requires thorough material analysis. An important indicator that can be utilized to gauge toughness is the ultimate tensile strength (UTS). This measures the ascertainable stress a material can endure when it is pulled or stretched before its fracture. This is very crucial in the manufacturing disasters of aerospace components, the construction of aerospace infrastructures, and UTS is required in consumer goods manufacturing. This article covers the basics of ultimate tensile strength, its importance in material science, as well as the various industries that utilize this feature, and the real-world impact of this feature.
What is Ultimate Tensile Strength?
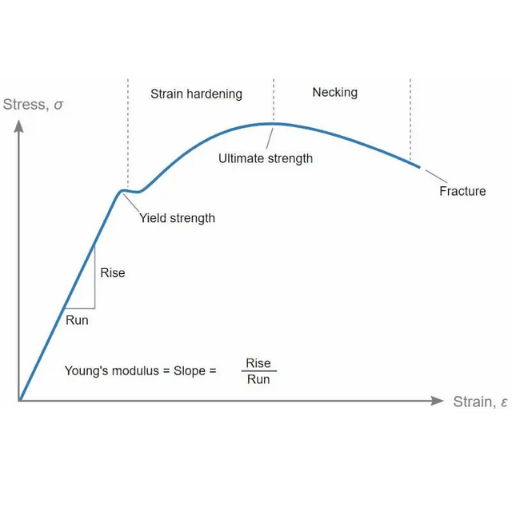
Ultimate tensile strength (UTS) is a measurement of the maximum stress a material can handle under tensile force before fracturing. UTS defines the limit of bearing capacity and performance evaluation of the material. It is expressed in pressure units, typically MPa or psi. UTS is determined by performing tensile tests using specialized devices that create controlled tensions until the specimen breaks. The value of UTS retrieved from the test helps engineers and scientists in all appropriate material selections for a given application.
Defining Ultimate Tensile Strength
Based on the most recent information, Ultimate Tensile Strength (UTS) is a specific form of tensile stress which peak at a materials breaking point when pulling or stretching said material. UTS is critical for determining the reliability and suitability of a material for specific applications.
Importance of Ultimate Tensile Strength in Engineering
In Advanced Engineering, extremes of stress and load borne by materials is studied. Thus, Maximum stress, also referred to as ultimate tensile strength of a material, heavily guides design decisions at every architectural and mechanical step to ensure endurance and functionality.
Factors Affecting Ultimate Tensile Strength
The ultimate tensile strength (UTS) of a material is influenced by its composition and external conditions during and after processing. Knowledge of these factors is critical when considering materials for a particular application or when attempting to engineer materials suited for a particular purpose. The most important factors that alter UTS are given below with some supporting data and details:
Factor | Impact on Tensile Strength (UTS) | Supporting Data |
---|---|---|
Material Composition |
Chemical makeup and microstructure dictate UTS. Alloys like steel achieve higher UTS due to elements like carbon, manganese, and chromium. |
High-carbon steel: UTS > 1,200 MPa; Low-carbon steel: UTS < 400 MPa (Materials Science Journal, 2023). |
Processing Methods |
Heat treatment (e.g., quenching, tempering) modifies grain structure to increase strength. Cold working induces strain hardening. |
Cold working increases strength by up to 30% (ASM International, 2022). |
Temperature and Environment |
High temperatures reduce UTS; corrosive environments degrade strength over time. |
Stainless steel retains 70% UTS at >700°F (371°C) (NIST). |
Grain Size |
Smaller grains enhance UTS via the Hall-Petch relationship. |
Grain sizes <10 micrometers increase UTS by up to 50% (Journal of Metallurgical Engineering, 2023). |
Surface Defects and Impurities |
Surface imperfections and impurities reduce UTS by acting as stress concentration points. |
Aerospace-grade titanium alloys: UTS ~900 MPa due to impurity control. |
Rigorous scrutiny and optimizations allow engineers to accurately tailor materials to exact specifications for automotive, aerospace, and construction sectors, where the ultimate tensile strength remains a pivotal consideration.
How Does Tensile Testing Work?
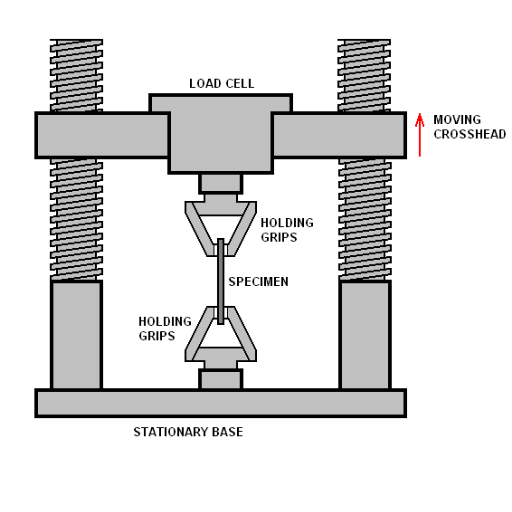
Overview of the Tensile Test Process
Tensile testing is a procedure wherein a sample of material undergoes force application until fracture. Testing begins with placing the specimen into a testing machine, which must be carefully aligned to avoid asymmetric stresses. With the specimen held in place, a constant force or extension rate is applied, with the machine recording changes in length and force resistance. UTS, yield strength, and elongation at break are then calculated. These mechanical parameters give an understanding of whether the material is appropriate for the intended engineering application.
Role of the Tensile Testing Machine
In contemporary engineering, the tensile testing machine is vital because it gives an accurate and systematic assessment of a material’s strength and deformation concerning its applied load, which significantly helps in its application and compliance with engineering standards.
Analyzing the Stress-Strain Curve
Key Point | Description |
---|---|
Proportional Limit |
Stress is proportional to strain (Hooke’s Law). |
Elastic Limit |
Maximum stress before permanent deformation. |
Yield Point |
Stress where plastic deformation begins. |
Ultimate Stress Point |
The maximum stress material can withstand. |
Fracture Point |
The stress at which a material breaks or fractures. |
What is the Difference Between Tensile Strength vs Yield Strength?
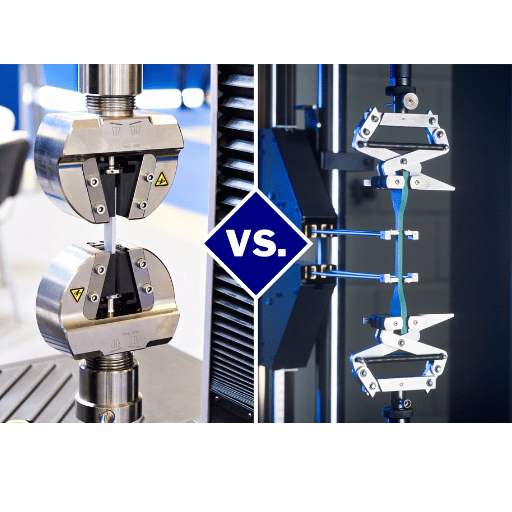
Understanding Yield Strength and Its Significance
Determining a material’s yield strength is critical in engineering since it indicates the maximum stress a material can endure before undergoing irreversible deformation. In simpler terms, it marks the turning point where a material’s behavior shifts from elastic recovery to plastic deformation.
Comparison of Tensile Strength and Yield Strength
Key Point | Tensile Strength | Yield Strength |
---|---|---|
Definition |
Maximum stress before breaking |
The stress at which permanent deformation begins |
Measurement |
Maximum stress value |
Minimum stress value |
Behavior |
Indicates the material’s breaking point |
Indicates the start of plastic deformation |
Stress-Strain Curve |
Peak of the curve |
Transition from elastic to plastic deformation |
Importance |
Determines the ultimate load capacity |
Determines safe load limit |
Applications |
Used for brittle materials |
Used for ductile materials |
Value Magnitude |
Higher than yield strength |
Lower than tensile strength |
Material Response |
Material fractures |
Material deforms permanently |
Testing |
Final stage of stress testing |
The initial stage of stress testing |
Units |
Measured in Pascals (Pa) or Megapascals (MPa) |
Measured in Pascals (Pa) or Megapascals (MPa) |
Impact of Yield Point on Material Performance
Setting specifications fundamentally determines the maximum stress a material can undergo without deleterious change. The yield point denotes the exact point where this stress is reached and hence directly correlates with material performance. This relationship holds prominence in design considerations and safety evaluations spanning multiple engineering disciplines.
Why is Ultimate Tensile Stress Important for Metals and Alloys?
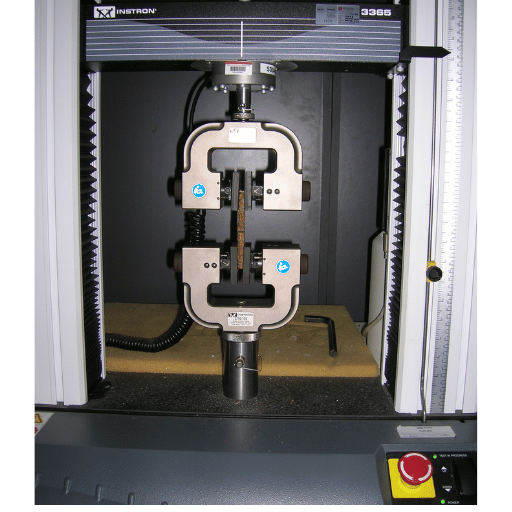
Applications in Steel and Other Metal Industries – Detailed Insights
The yield point acts as a critical factor in the steel and metal sectors as it impacts procurement, design enhancement, and quality assurance. For example;
- Structural Engineering: Steel grades like ASTM A36 and A572 are used in construction projects because their yield strength falls between 250 MPa and 450 MPa. This ensures that the structural elements will be able to support the associated loads without excessive deformation or failure, improving safety and durability.
- Automotive Industry: Advanced high-strength steels (AHSS) are frequently used in the construction of new automobiles due to their yield strength which is greater than 600 MPa. This allows for a reduction in material thickness while maintaining crash safety, enhancing fuel economy and lowering emissions.
- Aerospace Applications: Aluminum alloys of 7075-T6 are considered aerospace-grade with yield strengths of approximately 500 MPa, providing a favorable strength to weight ratio vital for aircraft components exposed to dynamic loads.
- Pipe and Pressure Vessel Manufacturing: Steel API 5L X65 is a pipeline grade steel with a yield strength of 448 MPa, therefore widely applied for pipeline systems. These materials can withstand internal pressures, avoiding fracture during oil and gas transportation.
Yield Point Data for Select Metals
Material |
Yield Strength (MPa) |
Applications |
---|---|---|
ASTM A36 Steel |
250 |
Construction, bridges, and buildings |
AHSS |
600+ |
Automotive components and body panels |
7075-T6 Aluminum Alloy |
500 |
Aerospace structures and frames |
API 5L X65 Steel |
448 |
Pipelines and pressure vessels |
Grasping the consequences of the yield point within different metals and using such understanding to their full potential is important in meeting the operational, safety, and economic efficiency benchmarks from an industrial perspective.
Influence on Material Properties and Design
Key Aspect | Impact on Material Properties and Design |
---|---|
Durability |
Determines product lifespan and reliability |
Strength |
Resists stress without permanent deformation |
Toughness |
Absorbs energy before breaking |
Elasticity |
Returns to shape after deformation |
Thermal Conductivity |
Manages heat transfer in products |
Weight |
Affects portability and usability |
Aesthetic Qualities |
Enhances visual and tactile appeal |
Sustainability |
Reduces environmental impact |
Cost Efficiency |
Balances material cost with performance |
Environmental Resistance |
Ensures performance under specific conditions |
Hardness |
Resists wear, scratches, and surface damage |
Fracture Toughness |
Prevents crack propagation under stress |
Modulus (Stiffness) |
Controls deformation under load |
Availability |
Impacts production scalability and timelines |
Brand Alignment |
Reflects brand identity and values |
Case Studies: Ductile Materials in Structural Applications
Material | Application | Key Properties | Cost Trends | Advantages |
---|---|---|---|---|
Steel |
Bridge construction |
High tensile strength, ductility |
Prices rebounding, down 10.5% YoY[^3] |
Ideal for dynamic loads, crack resistance |
Aluminum |
Aerospace engineering |
Lightweight, ductile |
Higher than steel, stable trends |
Reduces weight, maintains strength |
Copper |
Electrical systems |
High ductility, conductivity |
Stable, higher than steel[^3] |
Reliable for wiring, thin strand shaping |
Titanium |
Medical implants |
Ductile, biocompatible |
Expensive, stable trends |
Flexible, strong, biocompatible |
Reinforced Concrete |
Building foundations |
Steel-reinforced, ductile |
Cost depends on steel prices[^3] |
Earthquake resistance, structural integrity |
How Does Strain Hardening Enhance Mechanical Properties?
Exploring the Strain Hardening Region
Strain hardening, or work hardening, improves mechanical properties by strengthening and hardening a material through processes of plastic deformation. It is my understanding that during the deformation process in the strain hardening region, dislocations within the material’s crystalline structure undergo multiplication and interactions. Such interactions resist further dislocation movement, thus enhancing the yield strength and tensile strength of the material. It enables the material to resist additional deformation under applied loads, which is vital for many engineering applications where increased durability and performance are important.
Benefits of Strain Hardening in Material Science
Strain hardening enhances material performance by augmenting tensile strength, yield strength, and resistance to deformation, thereby improving durable advanced engineering applications.
Practical Applications and Examples
- Automotive Industry: Strain hardening is utilized in the production of car body panels and structural parts to improve crashworthiness and longevity while keeping the designs lightweight.
- Aerospace Engineering: High performance and safety criteria for aircraft such as fuselages and wings are equipped with strain hardened components, enabling a high strength to weight ratio.
- Construction: The use of reinforced steel in structures such as buildings and bridges has benefits from strain hardening, which enhances the load-bearing capability and makes it more resistant to stress fractures.
- Manufacturing Process Tools: Producting items using straining processes leads to various tools such as dies, molds, and cutting tools enduring strain hardening which extends operational life and reduces wear.
- Consumer Goods: Cookware and cutlery are made using stainless steel, which is strain hardened, increasing their useful life and making them harder to reshape and permanently deform.
- Energy Sector: Materials that undergo strain hardening are used in components for oil rigs, pipelines and renewable energy installations because of the need to sustain environmental and mechanical stresses.
- Medical Devices: The application of strain hardening to surgical tools and implants enhances their function in critical health care by improving durability and precision, enabling them to withstand the test of time.
- Defense and military equipment: Armor plating, weaponry, and other defense equipment derive benefits from reduction of structural weakening and damage by using strain hardened materials for improved impact resistance.
Frequently Asked Questions (FAQs)
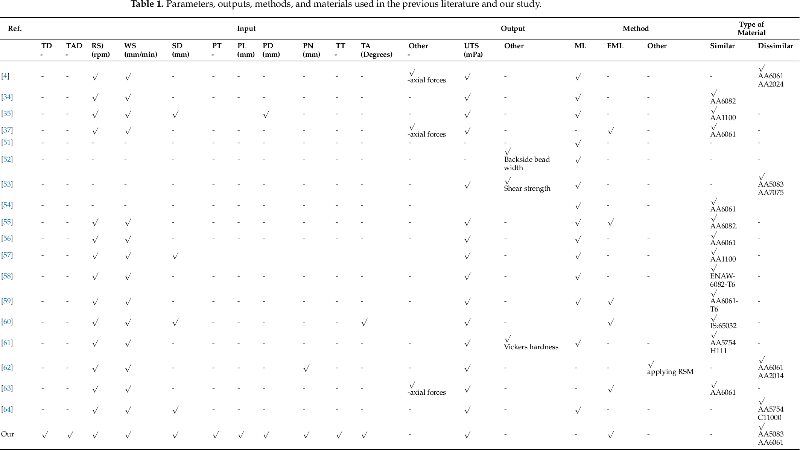
Q: What is Ultimate Tensile Strength (UTS), and why is it important?
A: The Ultimate tensile strength is the highest point of stress that a material can endure when it is being pulled to the point of fracture. It provides an aid in ascertaining the tensile attributes along with the qualitative power of the materials, which aids in predicting their performance in different situations.
Q: How is the tensile strength of a material measured?
A: The tensile strength of a material is measured through a tensile test whereby a test sample is placed under a pre-determined tensile load until it fails. The highest force of stress a material can sustain at that point is taken as the fracture stress and is expressed in units of either megapascals (MPa) or pounds per square inch (psi).
Q: What role does the stress-strain curve play in understanding material performance?
A: The stress-strain relationships are represented graphically, known as stress-strain curves, and provide critical insights into the performance of the material. It elucidates the association of force, stress (force per unit area), and relative change in length or deformation (strain). In addition to the elastic limit and associated yield point, regions of material undergo plastic deformation up to certain defined values of stress and strain.
Q: What undergoes a material when it is stressed beyond the yield point?
A: Materials undergo plastic deformation, meaning they will not revert to their original form once the stress is removed. The stress-removed shape is not equal to the original form because the shape is permanently deformed. The material will experience what is known as permanent deformation which is a result of surpassing the elastic limit.
Q: What is the effect of the cross-sectional area of a specimen on its tensile strength?
A: The cross-sectional area of a specimen plays a role in how the stress is applied to the specimen, as it tends to define the area where the load is also distributed. Also, it can be observed that the area has a certain limit, by observing that the ultimate tensile strength is lower for smaller cross-sectional areas than for larger cross-sectional areas, which means that it can bear more force.
Q: How are tensile strength and compressive strength different from each other?
A: The distinct difference between tensile strength and compressive strength is that one refers to the maximum stress a material while the strength refers to the maximum stress a material can withstand being pushed together. These distinctions permit the classification of the general strength of the materials when subjected to different types of loading factors.
Q: In what ways does the type of material affect how tensile strength tests are performed?
A: Different materials have different molecular structures and bonding which lead to distinctive tensile properties. The material choice is critical in tensile strength tests for accurate predictions in deformation, fracture response, or force resistance relative to real-world applications.
Q: What is the relationship between necking and a material’s tensile strength?
A: Necking happens when a material’s cross-section thins out considerably; thus, stress gets concentrated in a smaller region. This phenomenon diminishes the material’s ability to bear additional stress and reduces its overall tensile strength, leading to fracture.
Q: Explain the flexural strength of a material with high tensile strength.
A: Flexural strength primarily focuses on bending forces, whereas tensile strength deals with stretching. While a strong material suggests good resistance to elongation, it does not ensure high flexural strength. The correlation between tensile strength and flexural strength differs depending on material makeup and design.
Q: Why is it important to understand the regions of the stress-strain curve?
A: It is important to understand the regions of the stress-strain curve because it reveals how a material responds to stress in terms of its elastic behavior, yield point, and ultimate tensile strength, among other characteristics. This is critical for developing materials that are meant to operate under particular conditions.
Reference Sources
1. Ensemble machine learning methods for prediction of ultimate tensile strength (UTS) of asymmetric friction stir welded components (Matitopanum et al., 2023)
- Publication Date: 2023-01-27
- Key Findings: The article focused on building ensemble machine learning algorithms with Gaussian process regression (GPR) and support vector machine (SVM) for predicting ultimate tensile strength (UTS) of friction stir welded AA5083 and AA5061 aluminum alloys. Their model significantly outperformed all other methods tested (random forest, gradient boosting, ADA boosting, and SVM and GPR), achieving 30.67% to 49.33% improvement in prediction accuracy. An implementation of a differential evolution algorithm to optimize the model’s decision fusion weight boosted accuracy by an additional 10.32% over weighted average ensemble learning.
- Methodology: FSW Parameters consisted of 11 friction stir welding (FSW) parameters which were used as inputs with UTS as a responding variable. The study comprised of three datasets, two for training (80%) and testing (20%) and a reserved one for validation.
2. Factors influencing ultimate tensile strength and impact toughness of 3D printed parts with application of fractional factorial design (Mazen et al., 2022, pp. 2639–2651)
- Publication Date: 2022-01-04
- Key Findings: The study focused on five factors including part orientation, layer height, extrusion width, nozzle diameter, and filament temperature, concerning the impact of 3D printed PLA parts’ ultimate tensile strength and impact toughness. Only part orientation demonstrated a significant effect with p=0.05 on both tensile and impact toughness. Horizontal orientation was identified as the optimal condition for both parameters.
- Methodology: For this research, a fractional two to the power of five minus one resolute design was applied, resulting in 16 samples, each of which was printed on a Prusa I3 MK3S. The instruments used for the measurements were tensile strength: Instron 3367, and impact toughness: Tinius Olsen 66. Data analysis was performed using ANOVA and normal probability plots. Regression equations were used to estimate the functions of part orientation for tensile strength and impact toughness, and validation tests confirmed the models.
3. Predictive modeling of the ultimate tensile strength for 3D printing polylactic acid (PLA) materials with varying orientations of print layers (Yao et al., 2019).
- Publication Date: 15-04-2019
- Key Findings: The authors have put forward a model for estimating the ultimate tensile strength of 3D-printed PLA parts with respect to the printing orientation. (No specific insights about the predictive model’s validity or the correlation of strength and orientation have been disclosed in the abstract).
- Methodology: Based on the abstract, it lacks conclusive details concerning the methodology, which is tailored toward developing the predictive method.
4. Mississippi State University – Investigating Strength and Stiffness
This page outlined the principles of ultimate tensile strength and its relevance in a comprehensive manner.
5. Princeton University – UTS Glossary
An explanation from the glossary section of Princeton University’s curriculum, which explains ultimate tensile strength in relation to stress and strain graphs.
6. Tensile Strength Testing in Welding
It outlines the concept of ultimate tensile strength in welding and material evaluation.