In oilfield activities or drilling jobs, every element serves its purpose for efficiency and safety. Among the essential components, a pup joint stands out as a vital but sometimes neglected component. So, what really is a pup joint? And why is it so important in the energy and drilling fields?
This guide will ultimately provide a clear explanation of pup joints, their purpose, types, their uses, and how they help render an operation successful. Whether you want to enhance upon an existing foundation or just learn on the job, this article provides a thorough overview so that you might recognize and appreciate such a critical tool. Read on to find out how pup joints simplify operations, foster in-field adaptability, and come prepared with industry norms on performance and safety.
What is a pup joint and its role in oil and gas drilling?
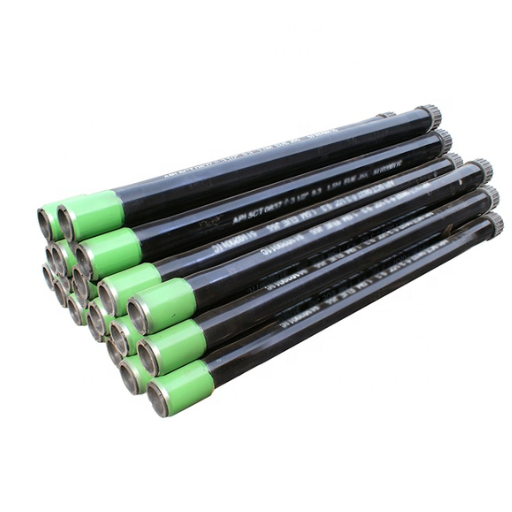
A pup joint is a relatively short pipe being used in oil and gas drilling operations to adjust the length of a drill string, casing, or tubing. The pup joint is chiefly used to set exact spacing in the wellbore for operational or safety reasons. Normally, these are fabricated from a tough steel, allowing them to resist high pressure and stresses exerted on them during drilling. These are made to keep alignment and connection integrity within a string to ensure efficient and safe drilling.
Exploring the basics of pup joints
Pup joints are essential parts in the oil and gas industry, playing an important role in drilling process optimization. They are available in varying lengths from 2 ft to 12 ft and sometimes longer. It is truly made so with respect to insertion inside a string assembly which relies on the distances for the exact adjustment of the pup joints inside a wellbore. Available in a premium grade material, such as high-strength alloy steel, pup joints can withstand high pressure, abrasion, and other extreme conditions that are characteristic of drilling operations.
In addition to ensuring mechanical integrity, pup joints also find variations in thread configurations to include API threads or premium threaded connections for their use with different tools and equipment. Their ability to connect and adjust tubular assemblies renders them invaluable for customizing solutions for varying well depths and formations.
Industry statistics report that quality pup joints lessen the risk of failure of connections and ease assembly while limiting non-productive time (NPT). These components, therefore, form part of operational standards, including API 5CT and API 7-1 certification, which further confirm their capability in the execution of major drilling operations.
Modern designs take it further by incorporating corrosion-resistant coatings and supreme precision machining for extended service life and enhanced performance. Improved durability means reduced maintenance costs; coupled with considerations for enhancement, these features for pup joints guarantee further advancement in well safety, and efficient operations coupled with long-term productivity.
How pup joints contribute to oil and gas extraction
Pup joints are tremendously important in oil and gas operations to lend flexibility and precision to drilling and extraction operations. These short pipe-type fittings adjust the length of the drill string or tubing according to well depths or configurations. Being able to maneuver the pup joint allows the operator to maintain proper spacing and alignment of the equipment that is necessary for smooth operations.
According to present data, a high-grade pup joint can resist pressures greater than 10,000 psi and temperatures beyond 300°F, thus being indispensable for severe condition operation in deep or offshore wells. High-end threading technology and premium material grade with solution heat-treated alloy steels of high tensile strength have improved the integrity of connection, hence reducing the potential of leakages or system failures.
The precise spacing facilitated by pup joints contributes to the unattached strain on mechanical components, thus aiding profitable hydrocarbon flow. According to some field studies, the use of pup joints suited for particular well environments can increase efficiency by up to 15%, with notable savings on costs and lower loss on downtime. Their continued compatibility with drilling components adds an extra layer of safety by supporting the structural integrity of the entire well system.
Such reliability, long life, and adaptability make pup joints indispensable in the oil and gas extraction industry, with each factor having a bearing on the aspects of productivity, safety, and, ultimately, operational success.
The significance of tubing pup joints in well completion
Tubing pup joints are critical components that determine the efficiency and flexibility of well completions. The components maintain the precise spacing between tubing sections, which is vital to establishing proper well performance. Since these pup joints are capable of bridging gaps in the tubular string, they help place tools and equipment downhole accurately, thereby maximizing alignment and lessening delays that could arise due to miscalculations or spacing errors.
Recent advancements in materials and manufacturing technology have had a positive impact on the performance of tubing pup joints. Increasingly, superior finishing is applied with high-grade alloys like chromium steel to withstand very high pressures and/or temperatures experienced deep down and also resist very corrosive constituents. Corrosion-resistant pup joints, for instance, may allow for an increase in service life for well tubing by about 30%, thereby lessening replacements with their associated maintenance costs.
Moreover, the data indicates that in higher geographical terrains, there’s an increase in the demand for tubing pup joints with improved connectivity features. Such innovations, including premium threaded connections, have been shown to enhance sealing and resist tensile and torsional stresses that are critical at higher depths. Thus, leading oil and gas product manufacturers now integrate such developments for changing well completion needs to ensure safe and efficient resource extraction.
Finally, industry insights suggest that 20% of the increase in operational efficiency during well completion is achieved by optimizing the use of tubing pup joints. This is an aftereffect of reduced installation time, decreased risks of tubing stress failure, and the ability to interface with advanced drilling technologies. By placing such highly durable components into the well system, operators preserve the asset’s structural integrity and strive to maximize its productivity with time.
How are pup joints manufactured and what materials are used?
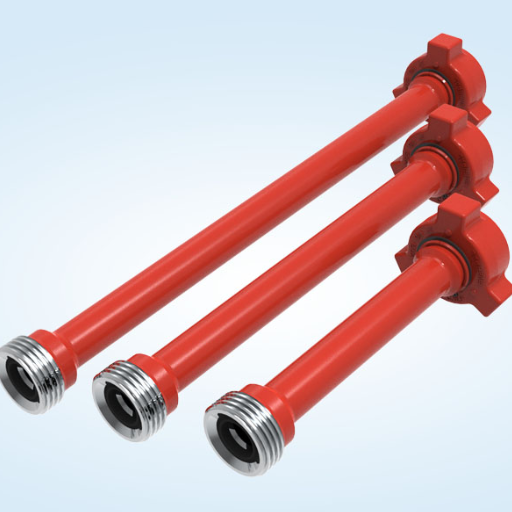
The pup joints are designed with materials under high-strength steel or alloy to guarantee that these are sturdy against any wellbore conditions. In their manufacturing processes, the steel tubing is cut at specific lengths with precision, and threading is given to the two ends so it aligns perfectly with other elements of the drill string. The threads manufactured are compared against industrial standards to ensure secure fitting and proper sealing against leakage. After threading, heat treatment is administered to further strengthen the joint and make it even more resistant to environment changes such as pressure and corrosivity of fluids. Interim to its sale, the pup joints are tested for quality assurance matters, inclusive of pressure testing and dimensional checks and tested for reliability and compliance against industrial specifications.
Overview of manufacturing processes
In the modern day, high-tech processes in the manufacturing industry have now rules out the need mainly depending on automated technologies to assure the user’s expected outcomes on precision, mechanics, and even uniformity. Automation is so beneficial in the provision of the machines, tools, the process of machining, defined using CNC, threads and quality controls. It has minimized errors and increased the capacity since it takes over the machine instead of a manual person controlling it. For instance, threading operations, which are currently using Computer Numerical Control (CNC) machines, were found to be capable of achieving extremely narrow tolerances like all the threads within ±0.005 inches, which has already been addressed and there is no longer any need to justify it over the long history of machining technology in the industrial world.
After that, heat treatment processes elevate parts well beyond on the surface of the material, as, in case of quenching or and tempering, continue beyond the limits of knowledge raises more questions about what the maximum strength figure could be rather exceeding that of the 110,000 psi claimed to have been achieved by some copper beryllium alloys after undergoing normal heat treatment procedures.
In addition, non-destructive testing (NDT) methods have availed ultrasonic and magnetic particle tests that can be reviewed by an NDT level ii personnel. Applied to the Aerospace, Nuclear Power, Defence, Oil & Gas, Marine, and Automotive Industries, these have enhanced surface and sub-surface defect detection for materials and product reliability.
There have been studies that suggest that 35% of such defects would be uncovered and remedied with the introduction of NDT in manufacturing resulting in fewer field failures and minimal downtimes for operators.
Another way of improving pup joint properties such as splash-zone wear and tear, out of gauge bore, galling, etc. resistance, reduced torque and resultant losses, and increased dog leg severity, is the use of improved materials and surface treatments. The use and performance of such coatings are further reported that cannon loaders being raymond cased and sintered hipped vehicle underbodies would use war separated coatings in the range of 5,000 home passes or higher.
As the timeframe is prolonged as the pup joint dwelling from the wellhead under the casing gradually deteriorates, advanced coatings particularly the plasma-spray ceramics are remedies because some geometries of the stabilizers at the upper shock level can cause even more than 10,000 pounds of compressive loads in the maintenance 1200 â 1300 ft/lb momentary threads.”
New trends in additive technologies, that is 3D printing, are also making advances in the field of the test and the manufacture of the components of the process. This also enables manufacturers to produce custom parts and prototypes with minimal material waste and significantly reduced amounts of time. Such developments therefore minimize resource wastages within the industry and every day bump the product quality and performance up to the evolving capacity of the many different industrial applications of the pup joints.
Key materials: stainless steel, carbon steel, and alloy
Stainless Steel
Stainless steel is one of the highly preferred materials for pup joints due to the superior resistance to corrosion it imparts, especially in adverse environments of high humidity, salinity, or chemical exposure. It is an alloy of primarily iron, chromium (at least 10.5%), and other elements such as nickel and molybdenum that add strength and durability. Common stainless steel types are 304 and 316; however, 316 is superior in resisting chloride corrosion and is therefore used more in offshore scenarios. Industry trends suggest that the stainless steel pup joints may take pressure and produce temperatures well in excess of 1500°F, lending safety and reliability in very demanding environments.
Carbon Steel
Carbon steel is preferred for pup joints because of its strength and the economy of its production. This material consists mostly of iron and carbon, and its properties vary with carbon content-higher carbon imparts strength but lowers weldability. Common grades of carbon steel include ASTM A106 or ASTM A333; the former is suitable for high-temperature services, and the latter best for very low temperatures. These grades, under appropriate circumstances, have been much used in oil and gas pipelines because they are capable of handling pressures well over 10,000 psi. Today, this steel can be treated with several surface treatments like galvanizing or epoxy coating, which adds to carbon steel’s life and performance.
Alloy Steel
Alloy steel offers a combination of excellent mechanical properties catered toward specific industrial application requirements. It is prepared by mixing carbon steel with other elements such as manganese, chromium, vanadium, or nickel, bestowing changes in the tensile strength, hardness, and wear resistance. Alloy steels typically used for pup joints would include AISI 4140 and 4340, known for their superior resistance to fatigue and are suited to pup joints highly stressed by heavy service. Tests have revealed that alloy steel pup joints can reliably operate at extremes of temperature and pressure, sometimes in excess of 20,000 psi. These high-performance attributes make them indispensable in critical applications such as deep-sea drilling and high-pressure hydraulic systems.
By understanding the peculiar features of stainless steel, carbon steel, and alloy steel, manufacturers and engineers can choose materials best suited for each operational need, thereby ensuring that pup joints will deliver the best performance, longevity, and cost savings in their various applications.
Pup joints are manufactured according to API standards
Recent developments in pup joint manufacturing have enhanced quality and performance. Pup joints nowadays get manufactured from state-of-the-art materials like high-strength steels and corrosion-resistant alloys and undergo rigorous testing to prove their merit under extreme pressure and harsh environmental conditions. These components stand to precise heat treatments and non-destructive testing methods such as ultrasonic inspection and magnetic particle examination for ensuring the greatest durability and safety in line with industry standards.
The data indicates that demand for pup joints has been steadily on the rise worldwide, mainly supported by the expansion of oil and gas exploration projects and newer hydraulic fracturing technologies. For instance, market reports show that premium pup joints capable of withstanding higher pressures have been witnessing a growth of over 20 percent for the last five years. Moreover, the strict adherence to API (American Petroleum Institute) codes continues to be an essential factor of production for ensuring uniformity and thus compatibility with other pipeline components.
Utilizing all these innovations, manufacturers have continuously raised the standard for quality so that the pup joints meet the ever-changing needs of the industry while providing better reliability and operational efficiency in vital applications.
What are the different types of pup joints?
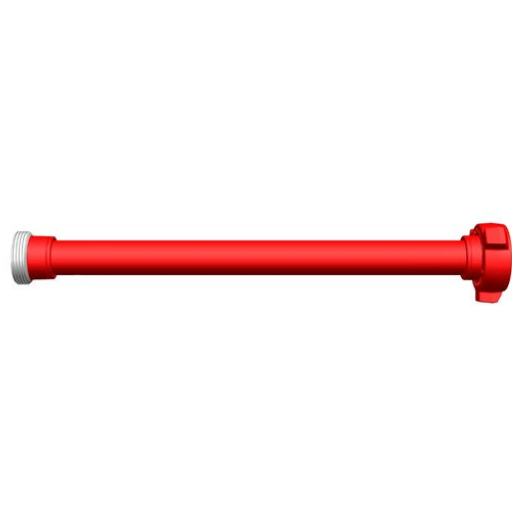
Pup joints lengths define the grade of the material used and their utility-specific application,some of the commonly seen types are:
- Standard Pup Joints – Used to change the lengths of tool strings or piping configurations. They correspond to a certain length required during the operation.
- Heavy-Wall Pup Joints- Used in situations involving high pressure and high stress; they are a little stronger and more durable.
- Crossover Pup Joints – As adapters between different sizes or threads, they provide resolution to different pipeline components, which are not compatible.
- Tubing and Casing Pup Joints- Mostly used for oilfield operations; they form a part of drilling and production setups; they conform to tubing or casing string sizes.
Each type is meant to maximize connectivity, alignment, and efficiency of various pipeline or drilling operations.
Differences between tubing pup and casing pup joints
The primary difference between tubing pup joints and casing pup joints lies in their size, application, and connection types, with tubing pup joints being smaller and used for production tubing, while casing pup joints are larger and used for well casing.
Parameter |
Tubing Pup |
Casing Pup |
---|---|---|
Size (OD) |
2⅜”–4½” |
4½”–20″ |
Length |
2–12 ft |
2–20 ft |
Grade |
J55, N80, L80 |
H40, J55, P110 |
Connection |
EUE, NUE |
STC, LTC, BTC |
Application |
Tubing strings |
Casing strings |
Wall Type |
Standard/Heavy |
Standard/Heavy |
Material |
API Steel |
API Steel |
Standard |
API 5CT |
API 5CT |
Understanding seamless vs. welded options
Pup tubes and pup casing joints can fare well or badly depending on the choice between seamless and welded pursuant to performance, durability, and cost. Seamless pup joints are manufactured by extruding solid billets, resulting in a homogenous structure free of welds. This makes the joints very safe in high-pressure and high-temperature conditions, where welds could fail due to weak points. Whenever tensile strength and resistance to corrosion rank over lesser strength or corrosion, the oil and gas industries prefer the seamless joint.
Welded pup joints, on the other hand, roll and weld flat steel into a cylindrical shape, with the welding line running across the length of the joint. Worldwide improvements in welding have also resulted in better welds. Therefore, as a cheaper option when high quality is not required, welded pup joints are now a contender. Welded pup joints bring the ability of being produced at a cheaper price due to the faster machining process, which may come handy in case of a project with tight budget constraints or a time crunch.
A more thorough juxtaposition turns out to be revealing from the perspective of performance. By industrial standards, the seamless type usually supports more stress with a burst pressure of around 20-30% higher than the welded. Welded joints could be adapted for a particular dimension or shape, and this eases their usefulness where multiple designs had to be considered.
Choosing between the two depends on the operational pressures involved, the type of materials requested, and the nature of the overall project. For example, high-pressure drilling favors seamless joints structurally, while the less-stressful application would capitalize on the reduced costs associated with welded.
Exploring API casing and tubing pup joint specifications
API casing and tubing pup joints are designed in accordance with the standards set by the American Petroleum Institute (API), ensuring their reliability and consistency in oil and gas operations. These components are essential for connecting long tubing strings, adjusting lengths, or repairing damaged sections in both drilling and production environments. Below are some critical specifications and data points relevant to API casing and tubing pup joints:
- Material Standards: Pup joints are manufactured using high-grade steel or alloy material, such as J55, N80, L80, or P110, which correspond to various operational requirements, including high-pressure and high-temperature conditions.
- Thread Types:
- Common thread types for pup joints include API round threads (EUE and NUE) and premium connections for enhanced sealing and strength. These threads minimize fluid leakage and provide reliable joint integrity under extreme conditions.
- The industry also emphasizes compatibility, ensuring thread types align with the rest of the casing string for seamless integration.
- Lengths and Sizes:
- API casing and tubing pup joints are available in standard lengths ranging from 2 feet to 12 feet, ensuring flexibility across applications.
- Diameter sizes typically range from 2-3/8 inches to 4-1/2 inches for tubing pup joints and larger sizes for casing pup joints, meeting diverse operational needs.
- Performance Attributes:
- Burst and Collapse Pressure Ratings: Pup joints undergo rigorous pressure tests to confirm their structural integrity against external collapse or internal pressure surges.
- Tensile Strength: These joints are engineered to withstand high tensile loads, often exceeding API minimum standards for reinforced safety.
- Coating and Protection:
- Pup joints are often coated with protective finishes like phosphate or zinc, enhancing corrosion resistance in harsh environments.
- Options for additional internal coatings are available to mitigate the impact of corrosive fluids and extend operational lifespan.
- Markings and Traceability:
- Each joint is distinctly marked with information including grade, size, weight, and thread type, ensuring proper identification and enabling supply chain traceability.
By adhering to these strict specifications, API casing and tubing pup joints deliver consistent performance and reliability, making them a staple in ensuring the safety and efficiency of drilling operations globally.
How do pup joints fit into the pipe and tubing system?
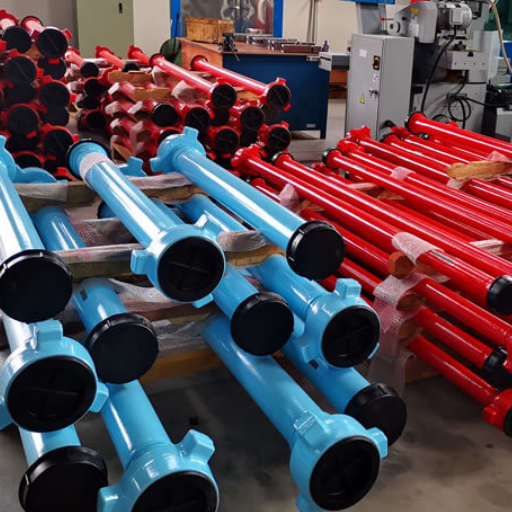
Essentially, pup joints link sections of pipe or tubing to obtain the wanted length for a system. They make up for length inconsistencies in sections of pipe, so the correct alignment and functionality can be made. By bypassing those gaps and allowing tight integrity with pup-joint connections, the whole piping or tubing system retains its integrity while operating efficiently. Because of their ensured accuracy in manufacturing and standardized sizes, these pup joint sets fit every configuration, thus becoming a backbone in operational accuracy and efficiency.
The role of coupling and connection methods
Methods of coupling and connection are vital in ensuring the reliability, stability, and efficiency of piping systems in industries. Proper connection methods enable the secure joining of pipes in a manner that does not form any leaks and protects the structural integrity of the system. Threaded couplings, for example, are well-known for being easy to install and for resisting the pressures usually encountered in oil and gas applications. Studies have been performed to indicate that markets of good quality threaded connections withstand pressures exceeding 15,000 psi, further establishing their strength in hostile environments.
Corrosion-resistant couplings have been developed through advances in material sciences, such as those made from stainless steel or special alloys. They give a longer life span to the system, allowing piping systems to function very well in corrosive environments, such as offshore drilling rigs or chemical processing plants.
Flanged connections, which allow systems to undergo maintenance or modification pretty often, are yet another method that has earned popularity. The seal is reliable, and temperature extremes can be accommodated, from -320 °F to above 1,200 °F, depending upon the gasket material utilized. Hence, flanged couplings would lie in some hard environments of the petrochemical and power generation industries.
According to the data, coupling failure contributes almost 30 percent to the unplanned downtime of industrial piping systems. Proper connection methods and investment in the latest sealing technologies can reduce maintenance costs and increase productivity, underscoring the importance couplings and connection methods have in operational efficiency and cost-effectiveness.
Impact on length, diameter, and size management
Length, diameter, and size management in an industrial piping system are key factors in guaranteeing the status and operational efficiency of the system. Pipe dimensions directly affect the rate of flow, pressure controls, mass movements, and hence the performance of the entire system in a broad sense. For example-a larger pipe diameter causes a reduction in fluid velocity, which in turn reduces frictional losses and energy consumption. Research indicated that up to 20% can be saved on energy losses in fluid transport systems by optimizing pipe diameters.
On the other hand, getting length management right means proper alignment, imposing less stress on fittings and couplings. Misaligned length corresponded with improper couplings almost inevitably results in a compromise of sealing that later endangers leaking. Studies have shown that proper pipe alignment and dimension standardization result in a 15%-20% reduction in maintenance costs.
Emerging technologies in size management include 3D scanning and computational modeling that now permit industries to forecast how materials behave under conditions of interest and customize pipe designs accordingly. These development-oriented approaches foster installation accuracy and prolong system lifetime. Thus, industries can heed these modern tools to enhance pipeline efficiency and avert costly downtime and repairs.
Integration with drill pipe and other tubular structures
The integration of drill pipe and other tubular structures into pipeline systems demands precise engineering coupled with advanced technology to derive maximum performance. Drilling fluid and mechanical forces come through the drill pipe and must be compatible with the tubular structures to endure extreme stress and allow for operations to go on unhindered. Over the years, technological advances in materials such as high-strength steels and corrosion-resistant alloys have pushed these elements further into durability and adaptiveness.
The innovations in thread design and premium connections are vital in ensuring a strong linkage between tubular structures. For instance, Premium Class Connections (PCC) have been found to perform better under high torque and pressures than normal connections, thus mitigating the incidence of joint failures. New reports reveal that modern thread connections might offer up to a 30% increase in load capacity, directly targeting the industry’s core concerns: operational safety and efficiency.
Meanwhile, computational modeling tools offer a method of simulating complex conditions such as extreme temperatures and high pressures to ensure compatibility and efficiency in integration. Studies reveal these predictive tools to increase joint alignment accuracy by about 25%, thereby cutting operational delays and extending the joint life of pipelines.
The adoption of API (American Petroleum Institute) specifications plays a significant role in ensuring uniformity and safety across different pipeline systems. Uniform application of these specifications makes for compatibility of drill pipes with other tubular structures, even in varying operational environments, thereby lowering maintenance costs and enhancing performance. The industry is using this ultimate combination of materials, designs, and digital tools to reach out for finer integration and improved performance.
What are common challenges and solutions in pup joint usage?
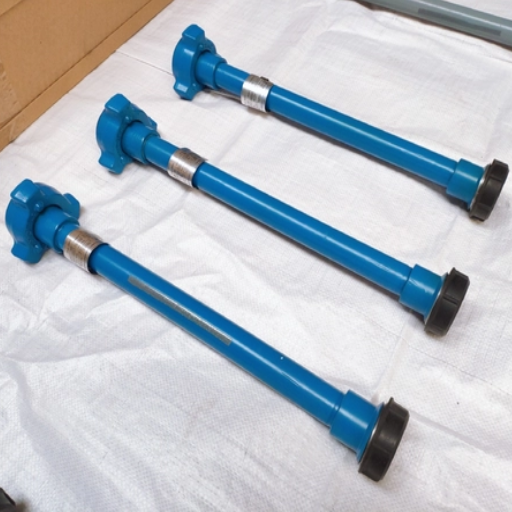
- Wear and Tear
- Challenge: Frequent usage can lead to surface damage, reducing the lifespan of pup joints.
- Solution: Regular inspections and the application of anti-corrosive coatings can mitigate wear and extend durability.
- Connection Integrity
- Challenge: Improper thread engagement or alignment can cause leaks or connection failures.
- Solution: Ensure proper handling during installation and inspect threads for damage before use.
- Material Fatigue
- Challenge: Repeated stress cycles may cause cracks or deformation over time.
- Solution: Use high-quality materials designed for high stress and replace fatigued joints promptly.
- Corrosion
- Challenge: Exposure to corrosive environments can weaken pup joints over time.
- Solution: Select corrosion-resistant materials and conduct routine maintenance to address potential issues early.
- Operational Compatibility
- Challenge: Mismatched specifications with other equipment can disrupt processes.
- Solution: Verify dimensional and pressure ratings to ensure seamless integration with the system.
Addressing repair and maintenance needs
Working toward repair and maintenance needs, I give priority to the periodical inspections so that any wear and tear can be detected early to avoid any sudden failures. I ensure that all repairs are promptly done using the best quality material, so their reliability is maintained. Besides this, I schedule maintenance sessions regularly to enhance life expectancy of components and avoid heavy-cost downtime, with operational efficiency being the prime concern.
Managing inventory and ensuring quality
Accurate record-keeping and frequent stock-level checks are done for good inventory and quality maintenance so that neither shortage nor overstocking ensue. I source good materials from reliable suppliers and make sure proper quality checks are carried out before acceptance of materials to meet the standards. Inventories are tracked systematically, and discrepancies are resolved orderly to ensure the smooth running of operations and consistency of products.
The coating technology and materials industry constantly experience emergent developments providing the industry with improved durability, performance, and aesthetics. An inventive generation of nano-coatings and self-healing finishes provide sublime barrier protection against corrosion, moisture, or abrasion, thus enjoying application within industrial, automotive, and architectural realms. In general, nano-coatings strengthen the surface at a microscopic level, thereby extending the product life and reducing maintenance cost.
Meanwhile, premium-grade materials, like high-strength alloys and environmentally friendly composites, have feverishly made their way to the forefront due to their superior performance and sustainability. Studies present that delineation industries using premium-grade materials have remarkably less waste of materials and energy consumption. Furthermore, the synergy of advanced coatings with these materials has enabled the fabrication of light and high-performing solutions, particularly for aerospace and renewable energy applications.
They also enjoy thermal barrier coatings to provide for machinery and building thermal insulation, so that for solar panels and consumer electronics there are anti-reflective, UV-resistant coatings. Firms engaged with such innovations see improved customer satisfaction, with respect to stiff competition in the market, thus testifying to the value of embracing such cutting-edge technologies.
Reference Sources
-
CiteSeerX – Design of NI sbRIO Based Working Fluid Level Detector and its Verification – Discusses the use of pup joints in sound velocity calculations.
-
ODP Leg 118 – Advances in Hard-Rock Drilling and Coring Techniques – Covers the application of pup joints in drilling operations.
-
American Journal of Veterinary Research – Transmission of Relaxin and Estrogens to Suckling Canine Pups – While not directly related to oilfield pup joints, it provides insights into the term “pup joint” in a different context.
Frequently Asked Questions (FAQs)
Q: What is a pup joint?
A: A pup joint is a short length of pipe used to adjust the length of a string of tubular goods to its exact requirement. They are often used in the oil and gas industry as an accessory to connect various pieces of equipment.
Q: How are tubing pup joints manufactured?
A: Tubing pup joints are manufactured according to API Spec 5CT using prime API monogrammed materials. They are typically made from seamless mechanical tube to ensure strength and durability.
Q: What materials are used for manufacturing pup joints?
A: Pup joints are commonly manufactured from seamless steel pipe to meet industry standards. High-quality materials ensure that these joints can withstand demanding environments.
Q: What are the applications of pup joints?
A: Pup joints are used in various applications, including as a spacer or reducer in tubing strings, to connect other piping components, or to adjust the length of a line pipe, riser, or sub. They are essential accessories in the construction and maintenance of pipelines.
Q: Are there different sizes available for pup joints?
A: Yes, pup joints are available in a range of sizes. This variety allows them to be compatible with different pipe diameters and meet specific operational requirements.
Q: What standards do pup joints adhere to?
A: Pup joints are manufactured according to API Spec 5CT, ensuring they meet the rigorous standards set by the American Petroleum Institute for safety and quality.
Q: What are the common end connections for pup joints?
A: The ends of pup joints are threaded to allow for easy connection with other piping components. This threading ensures a secure and leak-resistant fit.
Q: What is the significance of the API Spec 5CT in pup joint manufacturing?
A: The API Spec 5CT provides guidelines for the manufacturing of tubular goods like pup joints, ensuring they are produced using prime materials and meet industry standards for performance and safety.
Q: Can pup joints be used in sour service environments?
A: Yes, certain pup joints are designed to withstand sour service environments, which involve exposure to hydrogen sulfide. These joints are manufactured with materials that resist corrosion and maintain integrity under such conditions.
Q: Are there different types of pup joints for specific applications?
A: Yes, there are various types of pup joints, such as savers, spacers, reducers, and elbows, each designed for specific applications. They are essential components in customizing and optimizing piping systems.