When discussing construction and structural engineering, very few can rival the significance of the H Beam. Renown for great strength, versatility, and dependability, H Beams have become a pillar of numerous architectural and industrial projects across the globe. What, then, do steel marvels find so indispensable? Contractors, architects, or even those just curious-about-the-structures-molding-our-modern-world, will find this guide all about H Beams. From design to applications and benefits, we will go over the footprint of what makes them a ubiquitous industry choice. Get ready to learn more about enhancing structural solidity and changing your next project with H Beams!
Understanding H-Beams and I-Beams
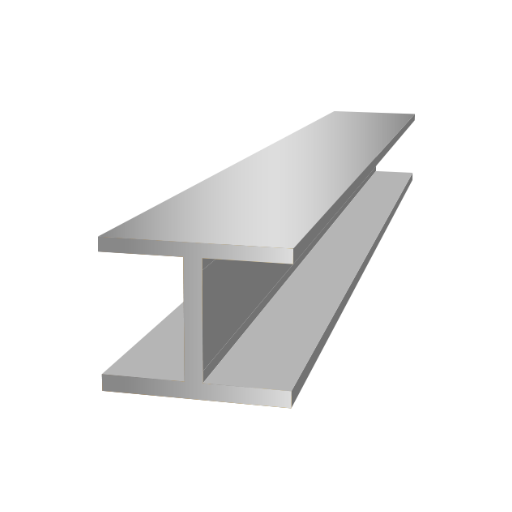
H-Beams and I-Beams are explicit structural components used in construction thanks to strength and versatility. Though their design parallels load-bearing capacity and final utilization, they differ almost totally.
- The flanges of an H-Beam are wider, and the web is thicker; hence it is suited for heavier loads and longer spans. The shape of an H-Beam is closely associated with that of an “H,” and it affords much structural integrity for projects requiring a ton of support.
- In contrast, I-Beams have a narrower flange and thinner web, looking like a letter “I.” I-Beams are light relative to H-Beams and are preferred in construction projects where weight saving is paramount, along with adequate strength.
Both beams are used throughout various structures: building, bridges, and even industrial frameworks. The choice depends on what load is required and the design criteria of a given project.
Definition of H-Beams
Structural steel beams that resemble the letter “H” in cross section are called H-beams or wide flange beams. The primary feature of H-beams is their broad flanges and wide web, providing them with maximum load-bearing ability and structural stability. The design enables the weight to be distributed along a wide surface area, making H-Beams a choice in heavy-duty construction.
H-Beams are majorly employed for massive construction in high-rise buildings, bridges, warehouses, and industrial framework. The most widely used sizes range from 100 mm to more than 1000 mm in height, and custom sizes can be fabricated to suit particular project requirements. Since these beams are very strong, they are capable of carrying vertical as well as horizontal loads and resisting bending and shear forces better.
The high strength-to-weight ratio ensures reduced steel consumption, making projects economical. This very property also eliminates the need for excessive reinforcement, as compared to other types of beams. In addition, H-beams are mostly made out of ASTM A36 or ASTM A992 steel, which guarantees that the structure is long-lasting and reliable even in demanding environments.
Due to their wide availability in grades and finishes, H-Beams are also customizable for special requirements, including design for seismic resistance or for exposure in arduous environmental conditions. These beams still remain among the most reliable choices in both conventional and modern engineering solutions, finding a middle ground among strength, longevity, and flexibility for design.
Definition of I-Beams
An I-Beam, also often termed as Universal Beam (UB), is a structural steel beam fabricated to an I-shaped cross-section. The I-shape consists of two horizontal flanges connected by a vertical web, which offers the best load-bearing capability, effective weight distribution, and strength. The flanges resist bending moments, whereas the web carries shear forces, thus making I-beams very efficient for structural purposes.
I-Beams are manufactured in a wide range of sizes and materials like ASTM A36 steel, ASTM A572 steel, and ASTM A992 steel and are used in a variety of industrial applications like construction, automotive, and shipbuilding, excel to support floors, roofs, and bridges due to their high strength-to-weight ratio. For instance, structural I-Beams today can carry loads of thousands of pounds with very little material used, giving the beam an optimized cost-performance-benefit.
Newer fabrication methods in steel have produced light-weight yet very strong I-Beams suitable for seismic-resilient designs and green architecture. This versatility, coupled with the advancements in material science, shall always keep I-Beams as one of the solutions to ever-changing demands in engineering and construction. Moreover, standards like ANSI and EN codes offer guidelines, specifying tolerances, dimensions, and performance characteristics to ensure uniformity and safety in different applications.
Structural Support Provided by Each
The structural integrity and behavior of an I-Beam vary and can be based on type, material, and intended use. For example, steel I-Beams are designed efficiently for applications in construction where distributed loads must be borne, owing to their high moment of inertia and large resistance to bending. It has been proved that structural steel I-Beams can bear loads that range between 10,000 and 24,000 pounds per linear foot, depending on the factors relating to size and grade.
Aluminum I-Beams are making headway in industries demanding strength and reduced weight, such as aerospace and automotive industries. These beams have 1/3 densities of steels, with the tensile strength ranging around 200-300 MPa, and they are the best choice for construction in cases where reduction of total load is important.
Composite I-Beams made from carbon fiber-reinforced polymers push innovation further. Such composites provide remarkable ratios of stiffness-to-weight and resistance against corrosion and extreme temperature. With the help of the most advanced materials development, carbon fiber-reinforced polymer beams are capable of sustaining heavy load-bearing in very critical applications such as bridges and offshore platforms while providing a life span of up to 30 years with minimal maintenance.
Material properties combined with specific cross-sectional designs make each I-Beam serve their unique structural requirements, eventually leading to further improvisations in efficiency, safety, and economy in modern engineering practices. Future advancements in materials interlinked with research and development are hopeful for promising options.
Comparative Analysis of H-Beams and I-Beams
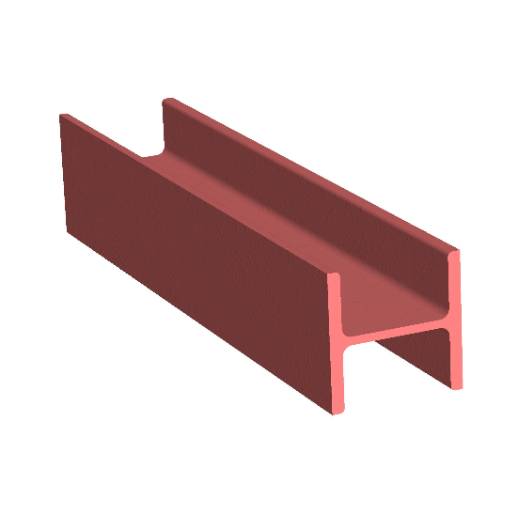
When comparing H-Beams and I-Beams, the primary differences lie in their design, application, and strength characteristics:
- Design:
- H-Beams have a wider flange, providing more surface area and stability. Their cross-section resembles the letter “H.”
- I-Beams feature a narrower flange and a more tapered edge, forming a shape similar to the letter “I.”
- Strength and Load Distribution:
- H-Beams offer better load distribution and can support greater weight over longer spans due to their broader flanges.
- I-Beams are more efficient for projects requiring strength in a specific direction, such as vertical loads.
- Applications:
- H-Beams are commonly used in large-scale construction projects, such as bridges and tall buildings, where high load-bearing capacity is essential.
- I-Beams are preferred for smaller-scale structures like residential frameworks and lighter platforms.
- Weight and Material Use:
- H-Beams generally use more material, making them heavier and more costly but ideal for sturdier construction.
- I-Beams are lighter and cost-effective, suitable for less demanding structural needs.
Both beam types are essential in modern construction, with the selection depending on project requirements, cost considerations, and structural demands.
Key Differences Between H-Beam and I-Beam
The key differences between H-Beam and I-Beam are their shape, strength, weight, span, and applications.
Parameter |
H-Beam |
I-Beam |
---|---|---|
Shape |
Wide flanges |
Narrow flanges |
Strength |
Higher |
Moderate |
Weight |
Heavier |
Lighter |
Span |
Up to 300 feet |
33-100 feet |
Applications |
Large structures |
Smaller projects |
Flange Design and Its Implications
The design of the flanges stands as a major differentiating parameter between H-Beams and I-Beams, thereby influencing their areas of structural application significantly. The flanges in H-Beams are comparatively wider and thicker, which brings along excellent load-carrying capacity and resistance against bending forces. Therefore, they find their use in enormous constructions such as industrial buildings where durability and strength are primary requirements, bridges, and skyscrapers. For example, an H-Beam having a flange width of 300mm can sustain lateral pressure considerably more than another I-Beam with a narrower flange width.
In contrast, I-Beams provide thinner flanges that taper toward their edges. This design saves on material weight, but at the same time, it limits the beam’s ability to withstand high torsional stresses. Hence, based on the I-Beam’s capacity, there are usually legitimate uses for it that include light and medium load-bearing applications such as floor and roof structures of the residential blocks. Studies have shown that a 50% reduction in flange width of an I-Beam translates into an approximately 30% weight saving, and this comes handy when the project emphasizes cost and material efficiency.
The choice amongst beam flange design varies depending on the conducted project, cost-effectiveness, and load conditions it expects. Adjusting the flange size optimizes and balances strength, stability, and material usage for both economic and structural specifications.
Load-Bearing Capacities
The load-carrying capacities of the structural beams depend on the material, cross-sectional design, and overall size. For example, Steel I-Beams are widely used in construction for their superior strength and durability. Their load-carrying capacity is mainly affected by the width of the flanges, the thickness of the web, and the length of the beam. For instance, a common steel I-Beam made out of A36 steel of 12 inches of depth and 10 inches of flange can carry loads exceeding 25,000 pounds over a 10-foot span.
Concrete beams, sometimes reinforced with rebars, load at very high potentials. Generally, based on reinforcements and mix design, a reinforced concrete beam of 8 inches standard depth and 12 inches width can bear loads ranging from 8,000 to 12,000 pounds over an equivalent span.
On the other hand, now progresses in composite materials-based technologies have brought lighter and thus robust alternatives. Therefore, efficiency in load-bearing composites fluctuates, with the highest load bearing ability varying between 4,000 to beyond 15,000 pounds depending on fiber orientations and matrix compositions.
To precisely consider the load-bearing capacities under specific conditions, engineers rely on specialized codes and computer tools, such as the finite element analysis, to develop optimized structures tailored to project specifications. Using these capacities becomes straightforward for using materials optimally while complying with safety standards.
Applications of H-Beams and I-Beams in Construction
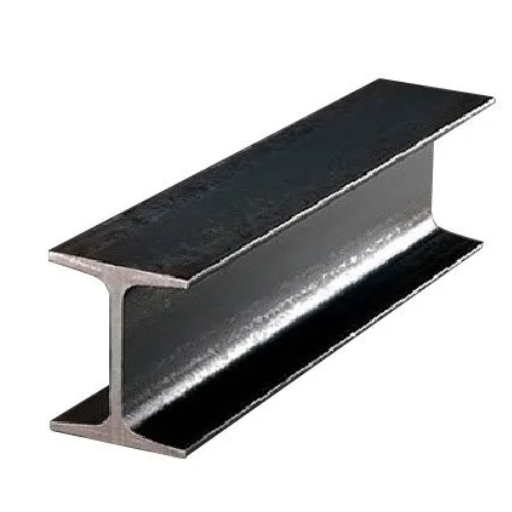
Due to H-Beams-I-Beams being strong and versatile and efficient in supporting heavy loads, they are heavily employed in construction.
- Due to their broader flanges and high load-bearing capacity, H-Beams are suitable for large-scale projects such as bridges, commercial buildings, and industrial complexes. The design permits these beams to support long spans effectively and carry heavy vertical loads.
- Similarly, I-Beams are mainly in use for smaller-scale projects such as residential housing and lighter structures. Due to the narrow flanges, they are best suited for supporting lighter loads and designing cheaper options for shorter spans.
However, these two types of beams are needed to create strong and durable frameworks while ensuring structural stability with minimum wastage of materials.
Common Uses of H-Beams
H-Beams find wide acceptance in construction and civil engineering owing to their superior strength and versatility. They are good in handling heavy vertical loads or for very long spans. The common uses of H-Beams include:
1. Commercial and Industrial Construction
H-Beams are the most basic key elements of constructing such huge structures like skyscrapers, factories, and warehouses. Their configuration facilitates greater load bearing capacity in the sense of withstanding loads of floors, roofs, and walls of multistoried buildings. In high-rise constructions, the H-Beams provide lateral stability to resist loads, both static and dynamic, such as wind loads.
2. Bridges and Overpasses
Mostly, H-Beams get used while designing the bridges and overpasses because of their lasting ability and capability to bear immense loads. H-Beams transfer loads across the entire system increasing safety and longevity. Also, in present-day-age bridge constructions, especially the long-span ones, H-Beams serve as chief members.
3. Heavy Machinery Support Structures
In industries installing large and heavy equipment, H-Beams create sturdy frames and foundations. These beams provided stabilization for machinery so that it can operate safely even under heavy operations.
4. Foundation Works and Pile Support
H-Beam is a good alternative for deep foundation works wherein the prevailing soil conditions require some form of reinforcement. They are generally driven into the ground as part of the pile structures to offer solid support in the long term for buildings and infrastructures.
5. Infrastructure Works
H-Beams are popular in infrastructure development such as railways and highways. They are used in building retaining walls, tunnels, and drainage systems to ensure reliability under different challenging environments.
6. Ship Building and Offshore Construction
The H-Beams find extensive application in building ships in constructing hulls and decks of the ships. Given their corrosion resistance and strength, they can hold up under harsh marine conditions. Similarly, offshore platforms of oil, as well as gas extraction, utilize H-Beams in their structural framework.
Common Uses of I-Beams
The beams with an I-shaped cross-section are widely recognized as I-Beams, H-Beams, or Universal Beams. Construction and engineering base many of their activities on these beams due to their great tensile strength and capability to bear heavy loads. Their adaptability has seen them ingrained into various applications.
1. Structural Framing in Construction
The I-Beams construct buildings, bridges, and commercial centers. It is an ingenious design that withstands a substantial amount of vertical loading for very little material and thus is cost-effective. Earlier, high-rise buildings had been prefabricated using I-Beam structures to ensure that they remain serviceable and stable under extreme conditions such as wind or seismic activations.
2. Bridge Construction
I-Beams are essential in bridge-building projects because of their durability and load-bearing capacity. They are particularly capable of standing up to heavy dynamic loads caused by vehicles. A case study of highway bridges in the US reveals that steel I-Beams are favoured for the long life they enjoy and the resistance to deformities over time.
3. Industrial Equipment and Platforms
Factories and industrial buildings use I-Beams in heavy equipment and platform construction. Since the I-Beams distribute weight effectively, they provide safety and efficiency in environments that operate heavy machinery or perform mechanical processes.
4. Residential Construction Reinforcement
In homes and smaller buildings where additional strength is required, I-beams are frequently used. They find significant use in supporting floors, ceilings, and even garages that require reliable load support for vehicles or equipment.
5. Railway and Transportation Networks
Being marvelously resistant, I-Beams play a significant part in railway developments, being tracks and bridges that bear the weight and repetitive stress of trains. Studies describe their employment in modern rail systems, particularly elevated track systems, as a trusted way for long-term infrastructure development.
6. Energy and Power Sector
I-Beams are often used by the energy power plants and renewable energy facilities for their need of secured framing and structures. For example, the wind turbine bases employ I-Beams to resist huge dynamic forces due to wind.
With their strength, I-Beams continue to innovate around a variety of industries, tackling complex engineering challenges with economics and sustainability.
Choosing the Right Beam for Your Project
Perfect beam selection for your construction requires evaluation of certain contingencies for maximizing performance and cost-efficiency. I-Beams, being popular for a variety of applications owing to their super strength-to-weight ratio, need users to be aware of the situations in which they must be used.
Key Factors to Consider
1. Load Requirements:
Consider the nature and magnitude of loads that the beam must bear. Static loading mainly includes that of machinery or roof; dynamic includes impact loading on bridges or wind turbines. These loads must be considered, so either the use of the I-Beams will provide the necessary strength, or else some other cost consideration will come into the picture regarding overdesign.
2. Material Selection:
Steel, aluminum, or composite materials make common beams. Steel I-Beams are highly preferred as they possess high tensile strength and durability; thus, they are most suitable for heavy industrial applications. In contrast, aluminum beams, being light and corrosion-resistant, are more suited to such lightweight construction as residential framework.
3. Span Length and Size:
If the span is longer, the size or strength of the beam should be increased accordingly to provide sufficient stability and evenly distribute the load. Standard steel I-Beams with a depth ranging from 10 to 18 inches can usually handle spans of 20 to 30 feet, based on load distribution particulars. If the span gets longer, options from the custom floor will come into play.
4. Environmental Conditions:
When an environment is harsh, i.e., coastal or industrial-type environment, beams should be treated with coatings to protect the beam from corrosion and wear. In such instances, galvanized steel I-Beams or powder-coated finish should be considered.
5. Sustainability goals:
The need to incorporate eco-friendly materials and designs into your project is in itself another condition. For example, steel beams are 100% recyclable and are often manufactured with an element of recycled content and thereby are awarded green building certification likes LEED (Leadership in Energy and Environmental Design).
Types and Sizes of H-Beams and I-Beams
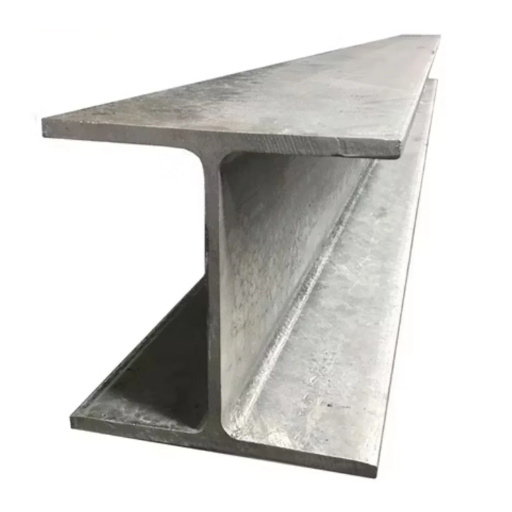
H-beams and I-beams come in various types and sizes, including H-beams (wide flange, HP-piles) and I-beams (standard, S-beams, W-beams), with dimensions ranging from 4″-16″ in width and depth, and lengths from 8′-40′.
Parameter |
H-Beam |
I-Beam |
---|---|---|
Shape |
“H” shape |
“I” shape |
Width |
4″-16″ |
4″-16″ |
Depth |
4″-16″ |
4″-16″ |
Length |
8′-40′ |
8′-40′ |
Flange |
Wide, parallel |
Narrow, tapered |
Web |
Thick |
Thin |
Strength |
High load |
Moderate load |
Uses |
Heavy structures |
Light structures |
Standard Sizes and Variants
Custom beam fabrication covers the entire spectrum of sizes and other variants to fit any building requirement. A beam is usually an I-beam, H-beam, or a T-beam, with each having its specific structural use. Standard I-beams are commonly between 3 inches and 16 inches in width and anywhere from 3 inches to over 50 inches in depth; large enough to be fitted into either residential or industrial works.
H-beams, with their wider flanges, carry heavier weight and are thus used in heavy-duty projects, such as building bridges and skyscrapers; widths can achieve as wide as 36 inches. Likewise, T-beams work together with I-beams in the support of precast structures, especially in floor systems.
Steel, aluminum, or composite beams may be chosen, depending on the application and type of custom beam required. The selection is thus dynamic. Steel beams, for example, are excellent in terms of ultimate strength and durability, whereas aluminum beams are used where weight is concerned. Prefabricated variants allow dimensional accuracy, load specification compliance, and efficient material-usage optimization, all resulting in cost reduction and maximized structural efficiency.
Wide Flange Beams vs. Standard Beams
Wide flange beams have wider, parallel flanges and thicker webs compared to standard I-beams, making them heavier but capable of handling greater loads and spans.
Parameter | Wide Flange Beam | Standard I-Beam |
---|---|---|
Flange |
Wide, parallel |
Narrow, tapered |
Web |
Thick |
Thin |
Weight |
Heavier |
Lighter |
Span |
Up to 300 ft |
33-100 ft |
Strength |
High load capacity |
Moderate load |
Material |
Multiple pieces |
Single piece |
Uses |
Heavy structures |
Light structures |
Custom Beam Fabrication Options
Planning custom beam fabrication is critical in making sure construction meets some particular structural and aesthetic requirements of the project. Industrial, commercial, or residential beams can carry intricate architectural designs involving varied load studies and site-specific constraints.
1. Material Selection
Custom beams can be fabricated from a wide range of materials depending on structural needs and environmental conditions. Carbon steel is chosen mostly for its good price and strength-to-weight ratio, whereas stainless steel is preferred when corrosion resistance is paramount because the project is exposed to moisture or chemical elements.
2. Precision Engineering
Laser cutting, CNC machining, and robotic welding are just some of the modern fabrication processes requiring superb dimensional control, with a tolerance of ±0.005 inches at critical dimensions, permitting the beam to fit into highly customized structures perfectly.
3. Varying Sizes and Shapes
Custom fabrication renders it possible to vary the height, flange width, web thickness, and length of H-beams and I-beams. For example, beams fabricated with depths ranging from 6 inches to over 48 inches cater for a variety of applications-from small residential frameworks to large-span industrial complexes.
4. Coating and Surface Finishes
Custom coatings can be applied to suit any durability and aesthetic requirement, such as galvanization, powder coating, or epoxy paints. For instance, with a galvanized coating, this provides good corrosion resistance and guarantees structural integrity in coastal or humid areas.
5. Application-Specific Solutions
With custom features, beams may be cambered or tapered for architectural reasons, castellated for profit in strength with diminished weight, and cellular with round holes to incorporate utility runs such as HVAC or electrical.
6. Productivity and Cost Efficiency
Newer technologies coupled with first-rate machinery have made processes in custom fabrication speedy and economical. Prefabrication minimizes project duration, material wastage, and onsite labor.
Custom beam fabrication is fast becoming an indispensable solution for present-day construction; with accuracy, adaptability, and improved efficiency, it aligns with the concepts of sustainability and long-term performance.
Benefits of Using H-Beams over I-Beams
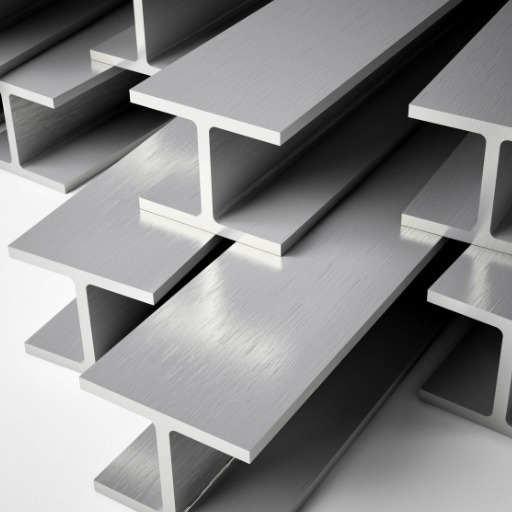
- Greater Load-Bearing Capacity: H-beams come with a wiser flange and web, allowing them them heavier loads and distributing the weight evenly than what Run-of-the-mill I-beams can do.
- Stability: H-beams afforded higher levels of structural soundness, an attribute that should thus be favored wherever a very large project or infrastructure is to be erected.
- Efficient Material Usage: Such materials are defined by the optimization of dimensions that conserve materials while granting strength and durability.
- Versatility: Owing to their capability of providing greater strength and stability, H-beams can be employed across a wide range of foundations, bridges, and high-rise buildings.
- Cost-Effectiveness: Due to their higher initial cost, H-beams over time will see lower costs in maintenance and replacement, owing to their strength and durability in supporting heavy loads.
Advantages in Structural Integrity
In my opinion, the H-beams stand out for providing superior structural strength and integrity. Being designed to equally disperse weight, stress on particular components is lessened, thereby reducing the chances of failure of the structure. Such reliability permits them to work under heavy loads and unfavorable conditions, making them truly right options for long-term projects. Moreover, having an equally strong web and flanges contributes to more stability, hence safety and durability across applications.
Cost-Effectiveness of H-Beams
For me, H-beams provide the best cost efficiency because their load-bearing capacity is superior, thereby reducing the need for any further support structure in addition to extra materials. The design itself uses steel for the utmost efficiency, resulting in the least steel wasted. Material costs are reduced, which in turn lowers the labor and installation costs-he-beams being therefore economically viable in long-term projects.
Installation and Welding Considerations
From my perspective, H-beams installation and welding are fairly simple if the correct procedures are followed. Due to their uniformity in design, they can be easily aligned and welded, thus, contributing to a shorter construction schedule. Using modern welding methods and ensuring strict measurement adherence, the structure’s strength and steadiness will be maintained with ease.
Market Trends and Innovations in Beam Design
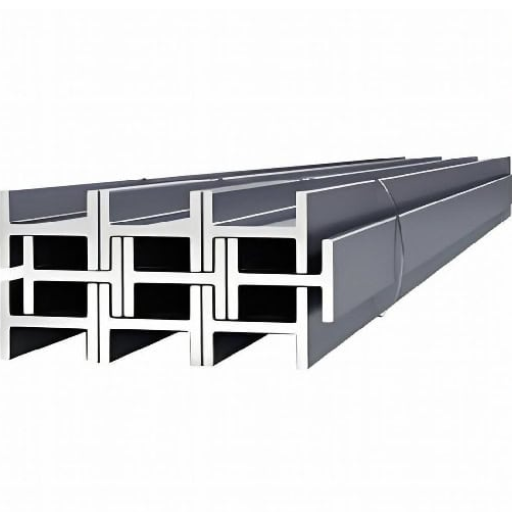
The design of beams is going through many advancements, from an interest in sustainable construction practices and more severe structural efficiency. Lightweight materials like high-strength steel and advanced composites are preferred because of the ability to carry loads with less weight. Modular and prefabricated solutions for beams also find more appraisal for shorter installation times and less labor costs. The finisher faces great changes with the advent of 3D printing for the manufacture of customized beam shapes tailored for strength and flexibility. Another innovative issue is that of smart beams with on-board sensor technology to facilitate real-time monitoring of structural health for improved safety and maintenance value. These developments answer to ongoing trends that weigh heavily upon the building industry that promotes smart, efficient, and environmentally conscious building.
Current Trends in Steel Beam Use
The increasing urbanization and sustainability need have led to the use of more advanced steel beam designs in modern construction. One such trend being the increasing usage and acceptance of HSLA steel beams. Industry reports state that the HSLA beams are becoming more popular as being a great alternative to the standard steel beams due to their very favorable strength-to-weight ratio, resulting in reductions in steel usage up to 20% while meeting strength requirements. This therefore makes them a favorable option for high-rise buildings and large infrastructure projects.
Environmental considerations are an important topic nowadays in the steel industry. Recycled steel now forms almost 30% of steel manufacture worldwide, a number that keeps on rising as companies strive to do their bit in minimizing resource diffusion. The usage of steel beams with prefabrication methods is also on the rise. These techniques allow the on-site construction work to be reduced by up to 50%, reduce waste, and bring forth cost predictability, something required in modern-day efficient construction.
Applications of smart technology in steel beam usage are behaving as a disruptive technology. Structural health monitoring systems embedded in smart beams provide real-time data on stress, vibration, and potential wear, reducing maintenance cost and improving safety. For example, research indicates sensor-integrated systems can identify faults 30% faster than conventional inspection methods.
Innovations in Beam Fabrication
In recent days, various agencies are seeking to revolutionize beam fabrication to improve efficiency, sustainability, and material usage. One leading innovation is the implementation of automated laser cutting systems that can cut with accuracy within fractions of a millimeter while slashing material wastage by as much as 20%. On the other hand, 3D laser scanning can facilitate pre-fabrication so the on-site fitting and installation of parts are more accurate.
Processes combining additive manufacture with traditional methods are up and coming, offering cost-effective techniques for lightweight yet sturdy custom creations that cut down manufacturing by almost 15%. AI-based quality control systems have also raised detection rates for defects, offering reliable products at consistent quality and less money spent on reworking.
These technologies thrust the beam fabrication into a production paradigm favoring energy-saving approaches. The new practices have allowed beam manufacturers to set new standards across the industry at large to keep up with the rising demand for smart, green, and cost-efficient solutions.
Future of H-Beams and I-Beams in Construction
Sustainable practices have increasingly become the emphasis of attention, with technological advancements paving the way for future opportunities in H-beam and I-beam construction. With global construction demands foreseen to increase by 35% till the year 2030, demand for structural steel, in tandem with innovative designs of H-beams and I-beams, will play an increasingly vital role in fulfilling these demands in a more proficient manner.
High-strength, low-alloy (HSLA) steel integration into beam production is one of the main areas of advancement. HSLA steel enables higher carrying capacities for both H-beams and I-beams with lighter designs that, in turn, save on materials without compromising structural strength. Industry reports have stated that these advanced materials can result in up to a 20% reduction of steel consumption plus an accompanying cut in embedded carbon emissions from construction projects.
Digitalization of manufacturing and construction through Building Information Modeling (BIM) as well as computerized beam design is currently rendering project planning processes smoother. BIM gives the ability to custom-design H-beam and I-beam sizes accurately according to the particular demands of the project; hence there is less waste and a shorter timeline. It has been observed that accounting for BIM workflows in the process of structural design can lower the cost of a project by 10%-15% while affecting an up to 25% increase in productivity.
The global push for sustainable development is another impetus for the reuse and recycling of structural steel. The average recycling rate of structural steel is in excess of 90%, which, coupled with further advances in steel treatment, renders H-beams and I-beams reusable. This is consistent with green building certifications such as LEED, hence preferring these beams for sustainable construction.
As innovations continue to bring changes in construction processes, H-beams and I-beams shall continue to be the mainstay supported by enhanced strength and efficiency under a better environmental footing to build the infrastructure of tomorrow.
Reference Sources
- Title: Overview of the design of the ITER heating neutral beam injectors
Authors: R. Hemsworth et al.
Journal: New Journal of Physics
Publication Date: 2017-02-21
Citation Token: (Hemsworth et al., 2017)
Summary:
This paper discusses the design of the heating neutral beam injectors (HNBs) for the ITER project, which are intended to deliver significant power to the plasma in a tokamak. The injectors are designed to accelerate and neutralize negative ions, which is more efficient than positive ions at the required energy levels. The paper outlines the complexities involved in the design, including the challenges of creating negative ions, minimizing electron co-extraction, and ensuring the components can withstand the harsh nuclear environment. The authors emphasize the need for remote maintenance due to the activation of components by neutron and gamma radiation. - Title: Bulk properties of the medium produced in relativistic heavy-ion collisions from the beam energy scan program
Authors: S. C. L. Adamczyk et al.
Journal: Physical Review C
Publication Date: 2017-01-24
Citation Token: (Adamczyk et al., 2017, p. 044904)
Summary:
This study presents measurements of bulk properties of matter produced in Au+Au collisions at various energies as part of the Beam Energy Scan (BES) Program at the Relativistic Heavy Ion Collider (RHIC). The authors report on multiplicity densities, average transverse momenta, and particle ratios, discussing the chemical and kinetic freeze-out dynamics. The findings contribute to understanding the phase diagram of nuclear matter and the transition from hadronic to partonic matter. - Title: Passive Beam Switching and Dual-Beam Radiation Slot Antenna Loaded With ENZ Medium and Excited Through Ridge Gap Waveguide at Millimeter-Waves
Authors: A. Dadgarpour et al.
Journal: IEEE Transactions on Antennas and Propagation
Publication Year: 2017
Citation Token: (Dadgarpour et al., 2017, pp. 92–102)
Summary:
This paper presents a novel antenna design that utilizes an epsilon-near-zero (ENZ) medium for passive beam switching and dual-beam radiation. The authors describe the antenna’s excitation through a ridge gap waveguide, focusing on its performance at millimeter-wave frequencies. The study includes theoretical modeling and experimental validation, demonstrating the antenna’s capability to switch beams effectively while maintaining high efficiency.
Frequently Asked Questions (FAQs)
What is the difference between an h-beam and an i-beam?
The difference between an h-beam and an i-beam primarily lies in their design and structural efficiency. H-beams have a cross-section that resembles the letter “H,” with wider top and bottom flanges compared to the web, providing greater strength. In contrast, i-beams have a more slender profile, which may allow for easier handling but often results in a lower weight capacity. When determining which beam to use, consider the specific requirements of your project, such as load-bearing capacity and beam depth. H-beams are typically made of rolled steel and are favored for heavy-duty applications in steel construction due to their robust design.
How are h beams manufactured?
The manufacturing process of h beams involves a series of steps, including melting steel, pouring it into molds, and rolling it into shape. The production typically utilizes rolled steel, which is then cooled and cut to the desired length. H-section steel is created by heating the steel and passing it through rollers to achieve the necessary dimensions. This process allows for the creation of beams with consistent quality and strength. Additionally, the bottom flanges of h beams are often thicker, contributing to their overall stability and ability to withstand larger weights compared to other beam types. Understanding the manufacturing process can help in selecting the appropriate type of structural steel for your needs.
Are h-beams stronger than i-beams?
H-beams are generally considered stronger than i-beams due to their design, which includes thicker top and bottom flanges. This configuration allows h-beams to better resist bending and buckling under load, making them suitable for heavy structural applications. While i-beams can be advantageous in certain scenarios, such as when space is limited, h-beams are often preferred for large steel buildings where strength is paramount. The larger surface area of h-beams also provides better lateral stability. When choosing between the two beam types, it’s essential to evaluate the specific load requirements and the overall design of the project.
What are w beams and how do they compare to h beams?
W beams, or wide flange beams, are similar to h beams but have a different profile that may be more advantageous in certain structural applications. Like h beams, w beams are made of rolled steel and have a cross-section resembling the letter “H,” but they often have a wider flange and a more tapered web. This design can improve the distribution of forces across the beam, making them ideal for specific types of construction. While h beams are typically used for their strength in heavy-duty applications, w beams may be preferred for projects requiring a more lightweight option that still provides significant support. Understanding the differences between these beam types will help you select the most appropriate structural elements for your building project.
What are the applications of h beams in steel construction?
H beams are versatile structural elements used in a variety of applications within steel construction. They are commonly employed in the framing of buildings, bridges, and other infrastructures due to their high load-bearing capacity and durability. H beams are also used in the construction of heavy machinery and equipment because their strength allows them to support significant weight and resist deformation. Additionally, h beams are often utilized in the formation of frames for steel buildings, providing essential support for floors and roofs. Their ability to withstand large forces makes them an ideal choice for various structural applications, ensuring safety and stability in construction projects.